Innovation and teamwork are important to any engineer, and Luke Miller, a recent graduate with degrees in Mechanical and Manufacturing Engineering, successfully used these qualities.
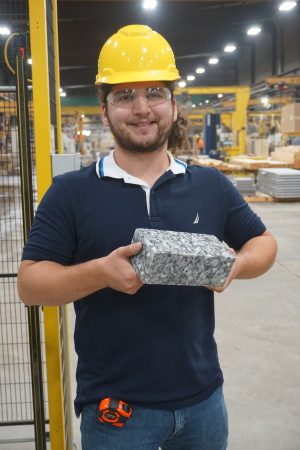
Miller spearheaded a project at Coldspring, a renowned granite manufacturing company. This project was born out of an engineering challenge, known as Huskies Invent, from St. Cloud State University’s College of Science and Engineering (COSE). In this event, Miller’s team created a solution to a persistent challenge concerning the placement of spacers on granite paving blocks. After Miller implemented the solution at Coldspring, it streamlined production, making a local industry more globally competitive.
Miller’s journey began during his junior year, when he participated in Huskies Invent, a 48-hour “inventathon” hosted by Coldspring. Miller said that he just wanted to sleep on the floor of the school for a night. Little did he know that this experience would shape his future career path.
In Miller’s account, he was skilled in drafting and his other mechanical engineering teammate, Stephen Keaton, was a “human encyclopedia” with a technical background in programing and testing. Another teammate, Sophie Tice, was talented in ideas and prototyping, while also delivering a strong white paper to Coldspring. Matthew McGough’s strength was social skills, which he used to call a company and ask questions about a system and an adhesive dispenser. He added professional experience and knowledge about how the industry worked. According to Miller, “We call came together to make a beautiful symphony of awesomeness!”
The City of Denver’s 16th Street Mall Project required precise application of spacers to 750,000 granite paving blocks to be used on Denver’s “main street.” Initially, his team experimented with various methods, including 3M glue tabs. However, these proved to be unreliable when subjected to side impacts. Determined to find a superior solution, the team delved into a research and brainstorming session. The eureka moment came when the team struck upon the idea of using hot glue on each granite paver, which could be adjusted in height and viscosity to function as the spacer itself. After the contest, Coldspring offered Miller an internship to work on implementing the proposed solution.
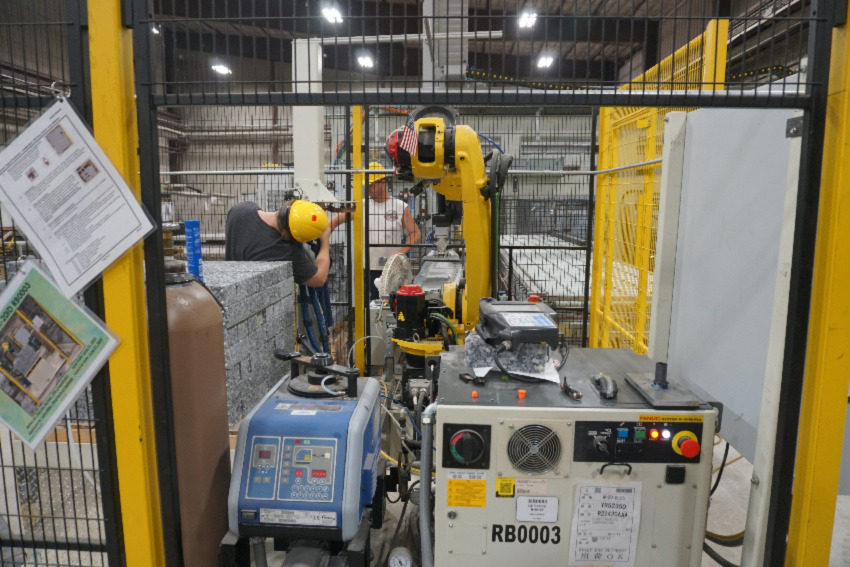
Over the course of the project, now at Coldspring, Miller collaborated with several companies in the region to acquire the necessary components for the robotic glue application system. Drawing from his engineering education and experience on his high school’s First Robotics team, Miller successfully implemented a gantry-style machine and integrated a robot for picking up the granite blocks, applying and curing the glue, and finally placing the granite blocks on pallets. This automated approach reduced complexity, minimized maintenance, and significantly improved the efficiency of the manufacturing process. This robotic system now takes only 27 seconds to apply spacers to each granite paver, far less time and with far higher quality than if people were applying them manually as competing companies in China do.
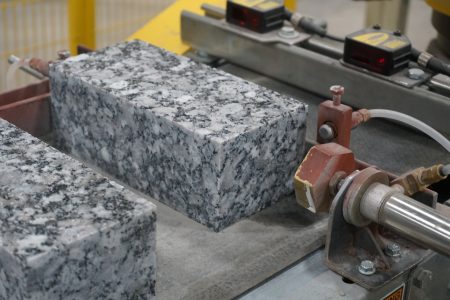
Impressed by Miller’s dedication and resourcefulness, Coldspring extended a job offer to him before he even completed his internship. They entrusted him with the continuation and refinement of the project. Throughout his senior year, Miller worked part-time at Coldspring, investing countless hours into perfecting the system. Fast forward to the present, and Miller is now a full-time employee at Coldspring. His project, once a mere concept, is now utilized in a multi-million-dollar project for the City of Denver.
Reflecting on this achievement, Miller admits, “Someday I’ll be out there on this street and looking at this project and feeling fondly about it. It’s very humbling.”